Если очень упрощенно представить структуру стали, то это матрица — пространственная кристаллическая решетка. В этой решетке есть вкрапления из высокотвердых частиц — карбидов.
Карбиды имеют прочность в несколько раз превосходящую матрицу.
Если мы режем только мягкие материалы, то достаточно ножа с низким содержанием карбидов. Но если необходимо работать, например, со шкурами, канатами и т.п., то клинок с низким содержанием карбидов очень быстро затупится, поскольку, как мы помним, матрица гораздо менее прочная.
Какой выход?
1. Увеличить прочность матрицы. Но тогда она станет хрупкой.
2. Увеличить размер карбидов. Однако выламывание карбидов из матрицы также приводит к ее быстрому разрушению и в конечном итоге — к затупливанию лезвия.
Единственный верный выход — это уменьшение размеров карбидов и увеличение их количества в матрице. Тогда выламывание некоторой части карбидов не приведет к затупливанию режущей кромки.
При этом размер карбидов напрямую зависит от скорости кристаллизации (то есть, от скорости охлаждения слитка стали при его производстве). Чем выше скорость — тем меньше размер карбидов. А традиционные методы металлургии уже исчерпали свои возможности в этом отношении — скорость кристаллизации увеличить не получается. Также имеются сложности с равномерным распределением легирующих добавок по матрице. Как следствие, — с равномерностью распределения карбидов по ней.
Суть порошкового переплава состоит в том, что расплавленный металл распыляется на мельчайшие частицы струей инертного газа. Этот процесс позволяет практически мгновенно кристаллизовать (охладить) сталь, то есть, она имеет твердое агрегатное состояние, но в виде порошка, а не слитка. Далее эту взвесь собирают, прессуют при очень высоких давлениях и спекают.
Таким образом, получается сталь с очень высокой карбидной фазой, равномерно распределенной по всему объему. Это гарантирует более высокую прочность относительно стали того же химического состава, но полученную традиционными способами.
Есть и еще один положительный момент. Порошковый передел стали позволяет увеличить количество легирующих добавок до уровня, недостижимого ранее.
Таким образом, в сталях порошкового передела успешно решены задачи увеличения количества легирующих добавок при их равномерном распределении.
Это, в свою очередь, приводит к образованию высокой карбидной фазы, а значит высокой прочности, износостойкости.
Все это положительно и очень существенно влияет на режущие свойства клинка из порошковой стали.
При этом порошковые стали отличаются друг от друга составом, твердостью, коррозионной стойкостью и для выбора ножа именно для ваших целей нужно изучить специфику предлагаемых вариантов. Тогда Вы будете довольны клинком из Vanadis или Elmax, а может и S390...
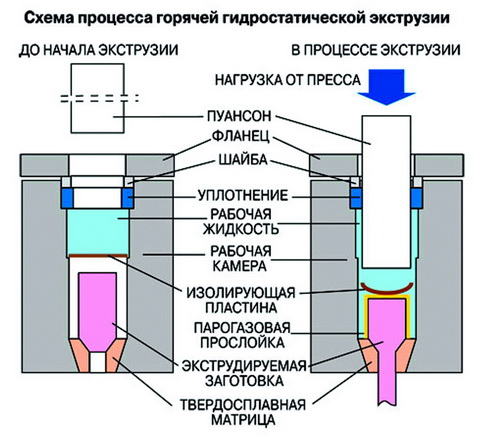
Задачи и решения
В конце XVIII века английский предприниматель и механик Джозеф Брама запатентовал конструкцию гидравлического пресса и предложил делать с его помощью свинцовые трубы продавливанием металла сквозь кольцевое отверстие матрицы, а в 1820 г. инженер Томас Бурр для этой цели построил специальный пресс.
К концу XIX века освоили изготовление экструдированием (то есть выдавливанием) уже медных труб и прутков.
Новый технологический процесс получил право на жизнь и стал быстро развиваться. Оказалось, что всестороннее сжатие заготовки пуансоном в контейнере повышает пластичность хрупких и малопластичных металлов и сплавов. Сегодня экструдирование горячих заготовок широко используется для получения из них прутков и профилей. Однако широкое применение этой технологии показало, что наряду с очевидными преимуществами она имеет и недостатки, затрудняющие ее использование.
Так, при экструдировании материала между ним и стенками контейнера, пуансоном и стенками матрицы возникает сухое трение, вызывающее интенсивный износ инструмента. Это, во-первых, удорожает процесс, а во-вторых, снижает качество поверхности и точность размеров готовой детали. Поэтому ее приходится дополнительно кали